ATI Press Releases
August 27, 2018
Discover speed and flexibility with VISION 5.2
Instrumentation Control Protocol (ICP) is the native default Accurate Technologies Inc. (ATI) proprietary communication protocol configured to the firm’s EMX Data Acquisition Module, offering a number of reliability and convenience benefits compared with conventional CAN acquisition. When connected to VISION Calibration and Data Acquisition Software via a VISION Network Hub or CANary CAN interface, an EMX module will communicate using ICP as its default setting.
Unlike some competitor data acquisition hardware protocols, ICP’s dynamic nature allows users flexibility when data logging multiple channels, whereby channels can be added or removed seamlessly within VISION at any time, while retaining data integrity. In addition, the frequency at which the channels are being viewed and recorded at can be altered in real time without requiring the recording to be stopped and restarted. Consequently, ATI’s ICP protocol ensures that users are able to work smoothly and efficiently and without interruptions to their progress.
Another advantage of ICP is that it offers a more efficient method of CAN based data acquisition. Traditional methods of data acquisition only include the time stamp within the software collecting the data, whereas communication via ICP allows for data to be time stamped immediately when the signal is measured within the EMX module. When sampling at higher speeds, this ensures that all the channels recording will display in the data viewer consistently, reducing noise in the data. This becomes increasingly important for those doing cause and effect analysis, who need to monitor precise timing of signals. In the same regard, those users will also benefit from the EMX’s simultaneously sampling data format, whereby every channel samples at precisely the same time, to provide an additional accuracy advantage. Below is a visual representation of the time stamp differences between pre-formatted CAN messages and ATI’s ICP over CAN mode.
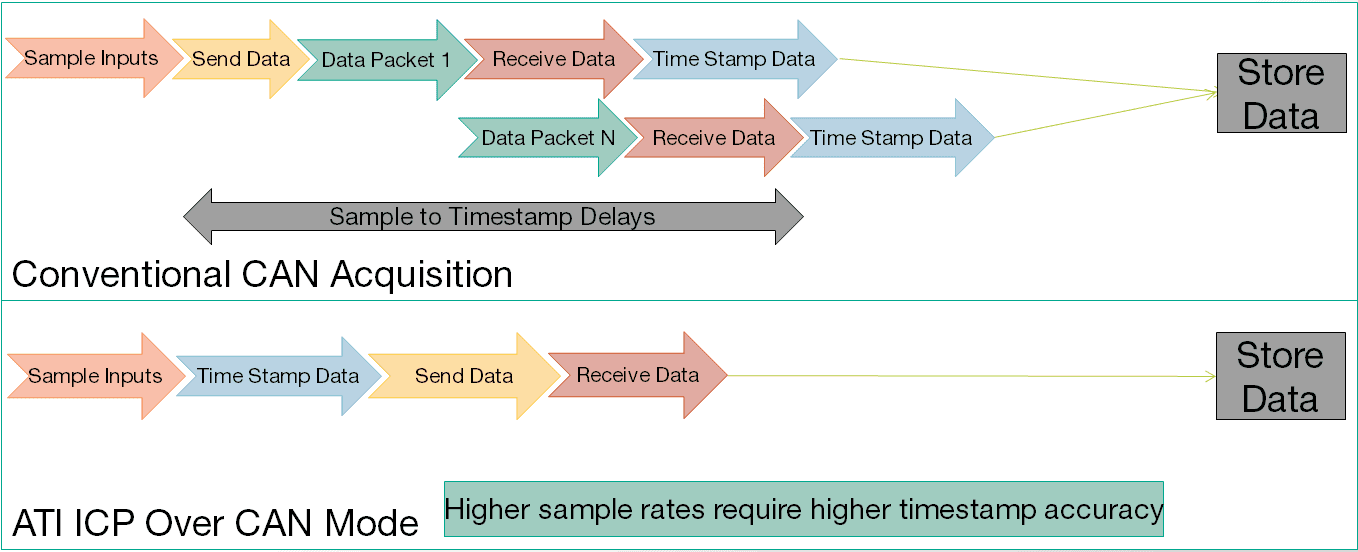
ICP is designed to integrate seamlessly into ATI’s VISION Data Acquisition and Calibration software, enabling users to exploit one of its key native features VISION - Filter Phasing Compensation. Typically, an unavoidable downside of filtering data is that the signal suffers from filter phase shift. When users are collecting data from multiple sources this can cause discrepancies in the actual time the signal was received relative to signals coming from alternative sources. Using Filter Phasing Compensation the data received in VISION is automatically corrected so that filtered data aligns perfectly with the raw data. This eliminates the need for post analysis of the recorded data, so users save time and work directly with the data received in VISION.
Below is an example on the effects of filtering data with conventional methods of data acquisition vs data acquisition with ICP over CAN.
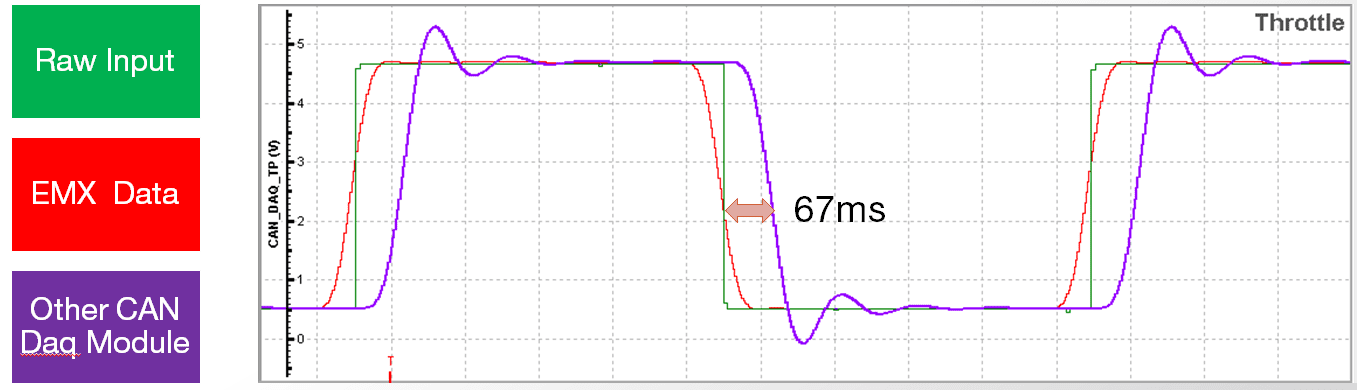
All of ATI’s products are designed to exceed customer needs, with the key design criteria always being an intuitive, easy to use format. As an extension of that philosophy, ICP provides users a faster and more flexible method of data acquisition over CAN through VISION’s automated configuration of the EMX. As a result, users no longer have to determine bit rate, CAN message ID or message format, because those functions are managed by VISION. This ensures users are running the optimized configuration offering the fastest method of data acquisition for their project.
Conventional CAN Acquisition
- Setup Software: Hardware Configuration Utility
- CAN Bit Rate: User defined
- CAN Message ID: Static (user defined)
- Data Items: Static (user defined)
- Update Rate: Static (user defined)
- Hardware Settings: Static (user defined)
- Data Timestamp: On message receipt
- Filter Phase Compensation: None
ATI ICP Over CAN Mode
- Setup Software: VISION
- CAN Bit Rate: Automatic
- CAN Message ID: Automatic
- Data Items: Dynamic
- Update Rate: Dynamic
- Hardware Settings: Dynamic
- Data Timestamp: When the input is sampled
- Filter Phase Compensation: Automatic
Taking advantage of ICP by using the combination of EMX hardware and VISION software allows users to reduce time lost spent correcting data captured by their DAQ hardware and software and instead enables them to focus on data actual capture and analysis, boosting productivity and providing a competitive edge for their project team.
Discover more information on VISION or EMX modules contact ATI sales at sales_us@accuratetechnologies.com
More Information
Below are links to products related to the above article.