E-MOBILITY
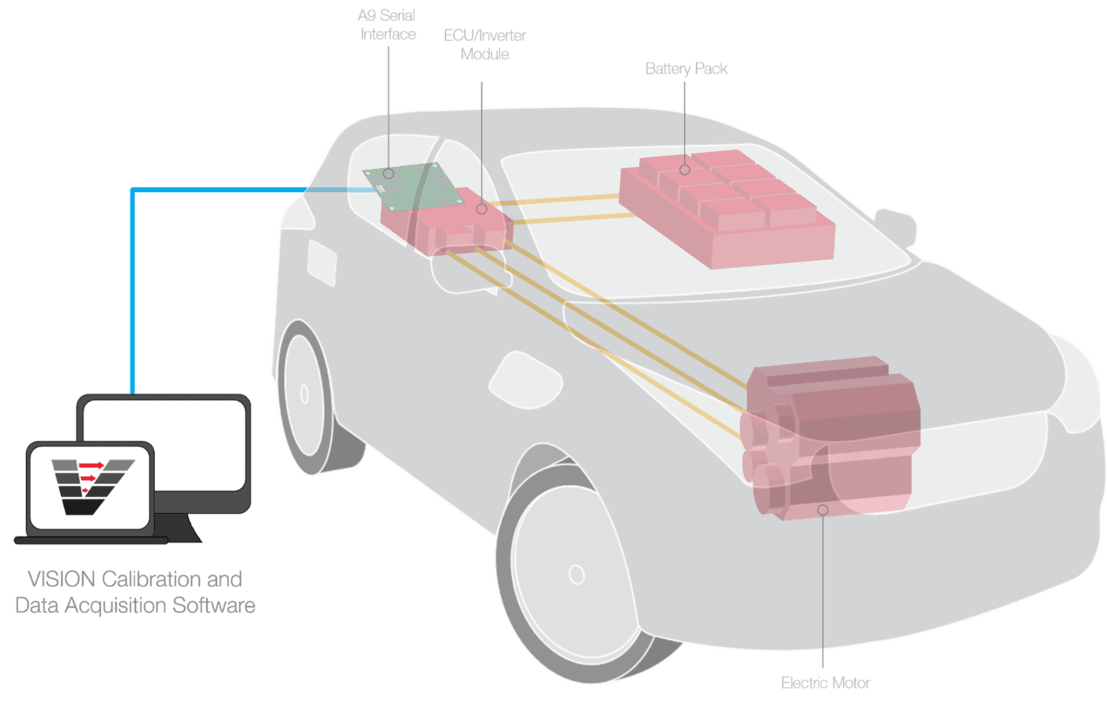
ECU Serial Communication
Battery Management Systems (BMS) Safe Operating Area (SoA) limits relying on CAN to deliver software interpreted hysteresis for a BMS, especially with High Voltage (HV), requiring a device faster than it’s capable of handling. Functional safety is of the highest importance in a BMS. It is critical during charging and discharging operation, to prevent the voltage, current, and temperature of any cell or module under supervisory control from exceeding defined SoA limits. HV systems for reading voltage/current of all cells exceed CAN bus speeds and cause indeterminate decisions. ATI’s A9 ECU Interface is capable of acquiring 125,000 data items, a sample Time period of 50us, and simultaneous DAQ Rates of 500+ independent data rates/raster by having direct communications with supported processors providing real time access to BMS data.
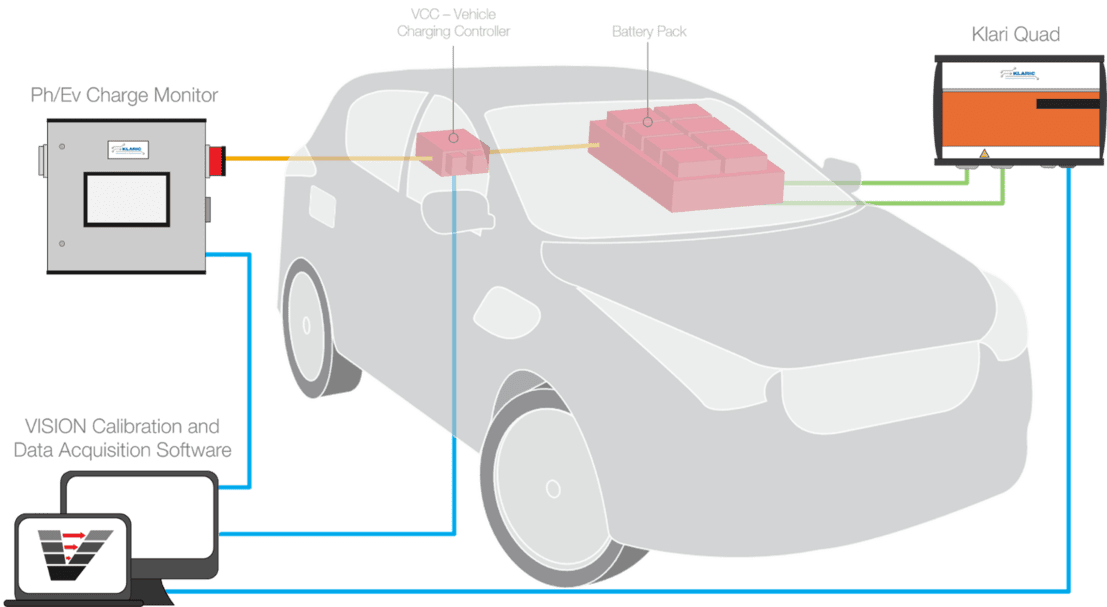

*Device dependent
*Device dependent
Charge Monitoring
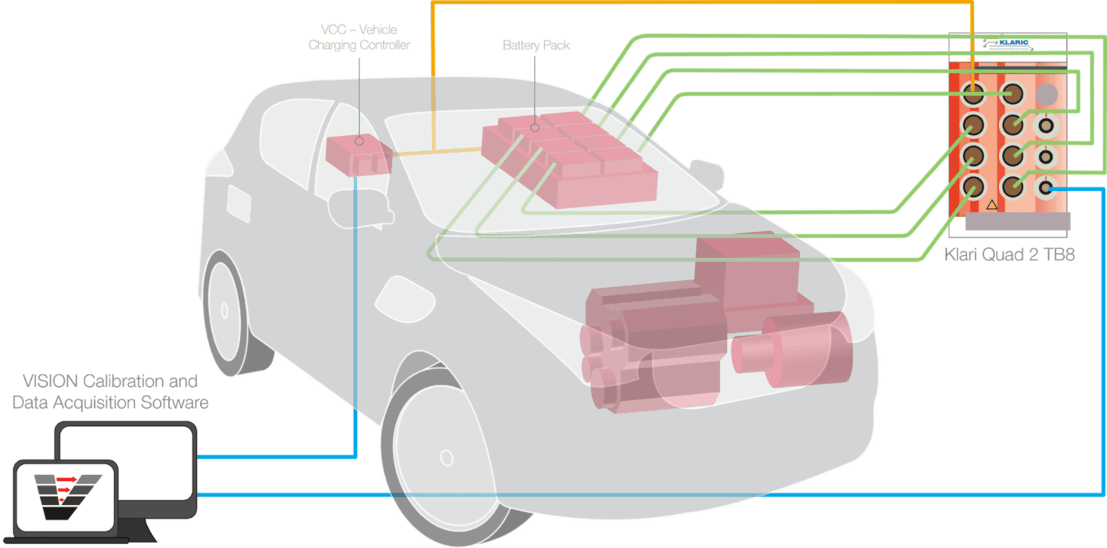

*Device dependent
*Device dependent
Battery Management Systems Testing
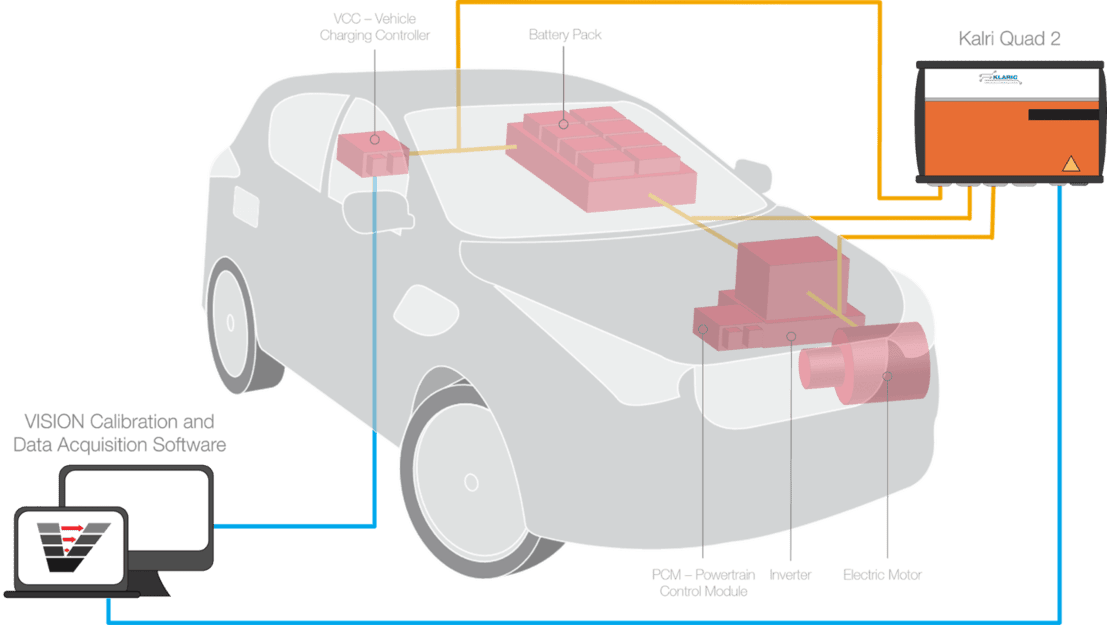

*Device dependent
*Device dependent
HV Powertrain Testing
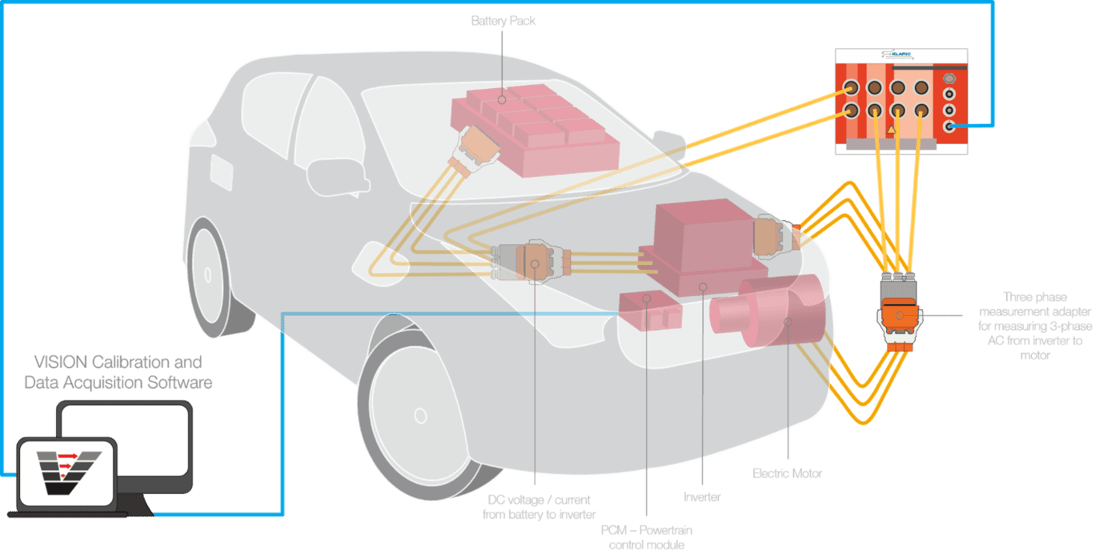

*Device dependent
*Device dependent
Motor / Inverter Efficiency Testing
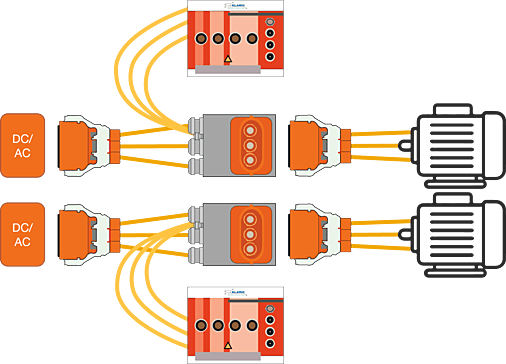
ATI/Klaric Solution
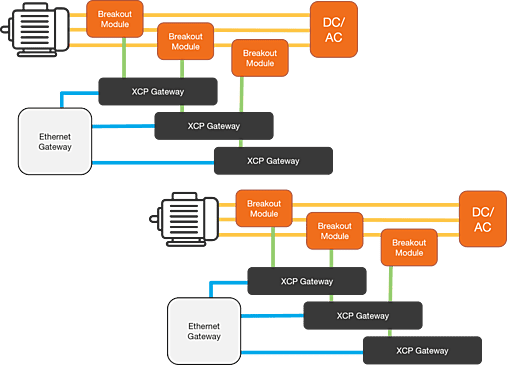
Other Solution
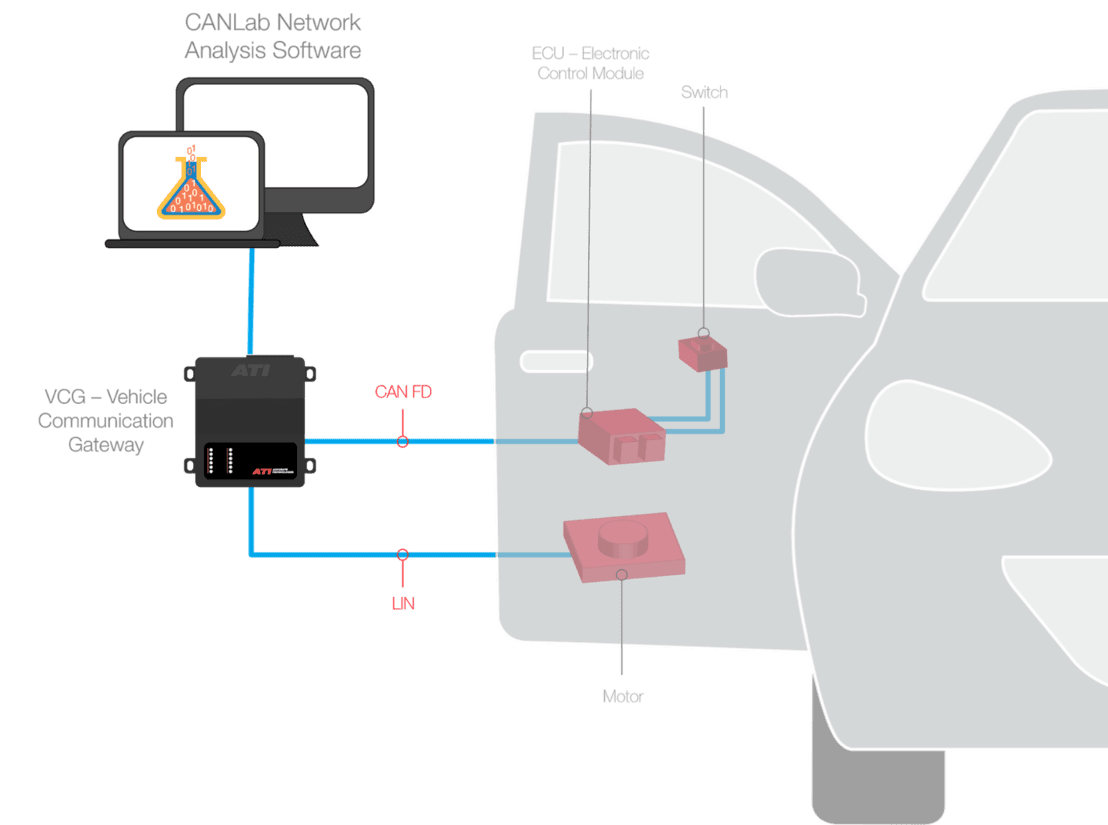
Cross-Protocol Communication
The VCG allows automotive engineers and technicians to establish communication with a vehicle's electronic control units (ECUs). This enables real-time monitoring, diagnostics, and data exchange with the vehicle's onboard systems. It can serve as a bridge between different automotive networks and protocols, including CAN, LIN, and Automotive Ethernet. This is particularly useful for analyzing and testing multi-network vehicle communication. Users can create custom testing procedures and scenarios. This flexibility is essential for assessing vehicle performance under specific conditions and for conducting validation and testing of new features.
More Information
Below are links to products related to the above application.