RS-232 has been a fundamental standard in serial communication for decades. Alongside RS-232, CAN (Controller Area Network) and Ethernet have become widely used interfaces in various industries, each offering distinct advantages. In this blog, we’ll explore the differences between RS-232, CAN, and Ethernet, and how Klaric’s integration of all three provides a significant advantage in precision measurement systems.
Understanding RS-232, CAN, and Ethernet
- Simplicity – RS-232 is straightforward to implement, making it a preferred choice for serial communication in various applications.
- Cost-Effectiveness – Due to its long-standing presence, the technology is affordable and easy to integrate.
- Short-Distance Communication – Ideal for reliable communication over distances up to 15 meters (50 feet).
- Wide Industry Adoption – Despite newer interfaces, RS-232 is still used in testing, automation, and industrial control systems.
- High Noise Immunity – Designed for industrial and automotive environments where electrical noise is prevalent.
- Multi-Node Communication – Supports multiple devices on a single bus, reducing the need for direct connections.
- Error Handling & Priority-Based Messaging – Built-in error detection and message prioritization enhance reliability.
- High-Speed Data Transfer – Capable of handling large volumes of data quickly.
- Scalability – Supports networking across long distances with high bandwidth.
- Flexible Topology – Unlike serial protocols, Ethernet allows for complex network structures.
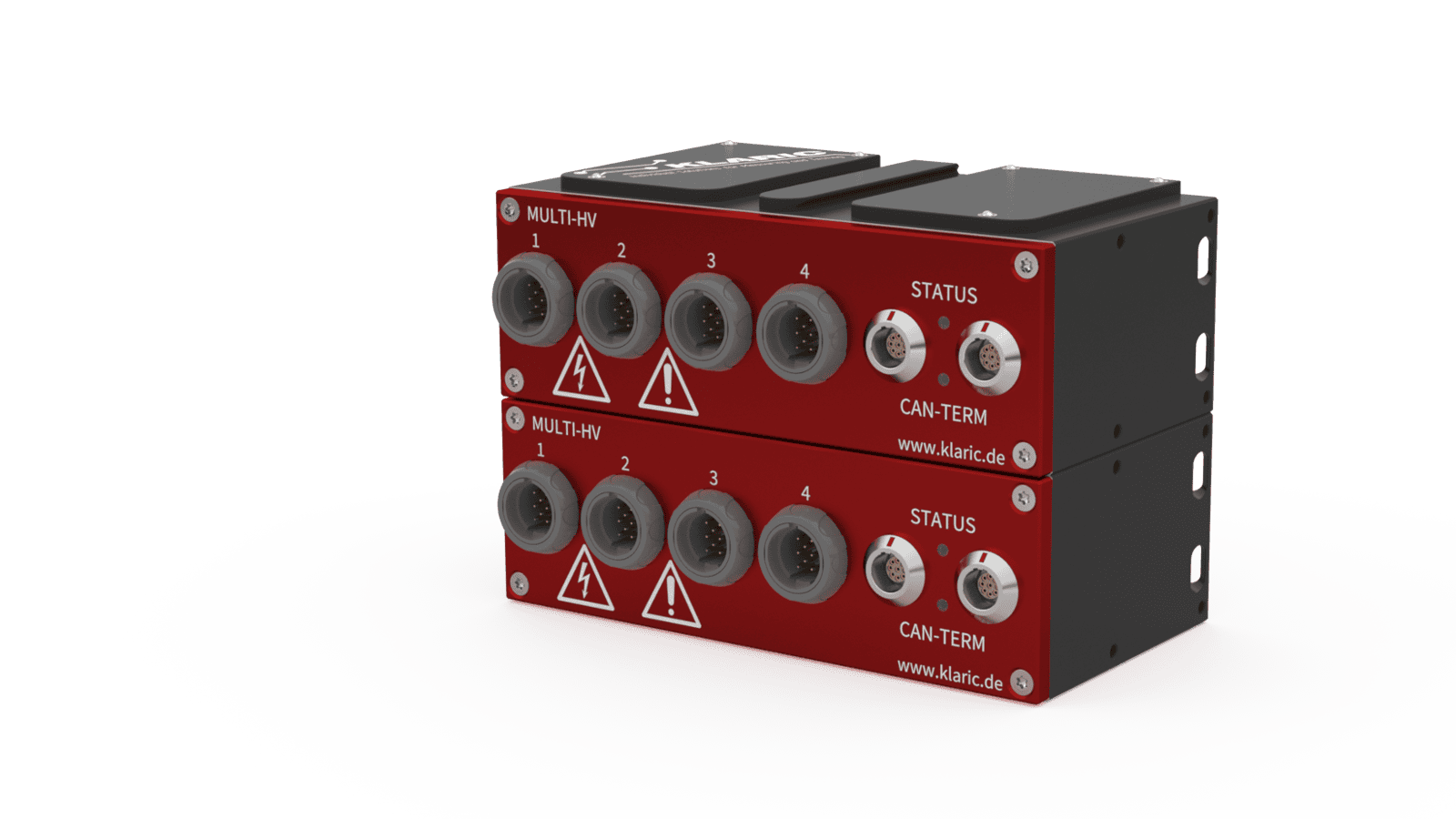
Klaric Hardware: The Advantage of Supporting RS-232, CAN, and Ethernet
Klaric, known for its precision measurement modules, integrates RS-232, CAN, and Ethernet to offer maximum flexibility. This multi-interface approach provides several advantages:
- Versatility – Users can select the most appropriate interface for their specific use case, whether it's automotive diagnostics (CAN), industrial automation (Ethernet), or simple serial communication (RS-232).
- Interoperability – Klaric devices can communicate with a wide range of equipment, from legacy systems using RS-232 to modern networks utilizing Ethernet.
- Robustness – By supporting all three protocols, Klaric ensures reliability across different environments, from high-noise industrial applications to high-speed data acquisition setups.
- Future-Proofing – As industries transition to newer technologies, Klaric’s multi-interface capability allows seamless adaptation without needing additional hardware replacements.
Conclusion
While modern interfaces like CAN and Ethernet continue to evolve, RS-232 remains a valuable choice for many applications. Klaric’s integration of all three technologies underscores its commitment to reliability, flexibility, and efficiency. Whether in automotive testing, industrial automation, or data acquisition, having multiple communication options ensures optimal performance in diverse scenarios.