Manufacturing
______
Commitment to Quality
ATI Quality
ISO 9001:2015 Certified Quality Management System
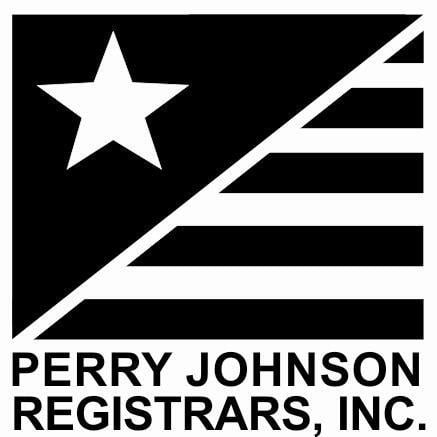
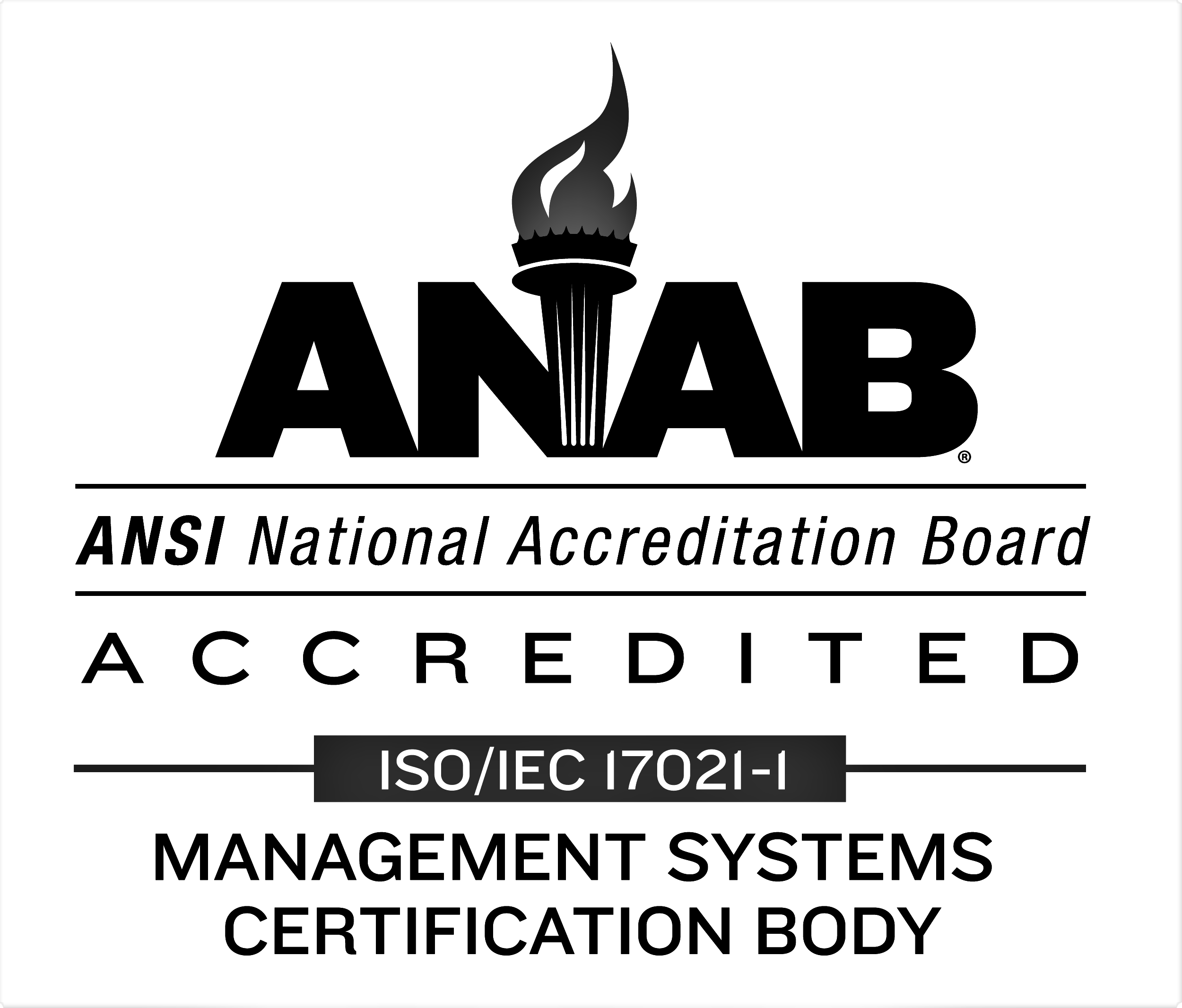
ISO 9001:2015 certification is maintained at our Manufacturing facility located in Novi, MI USA. Maintaining the certification is a true testament to our commitment to quality.
Design/Fabrication
3D Printer
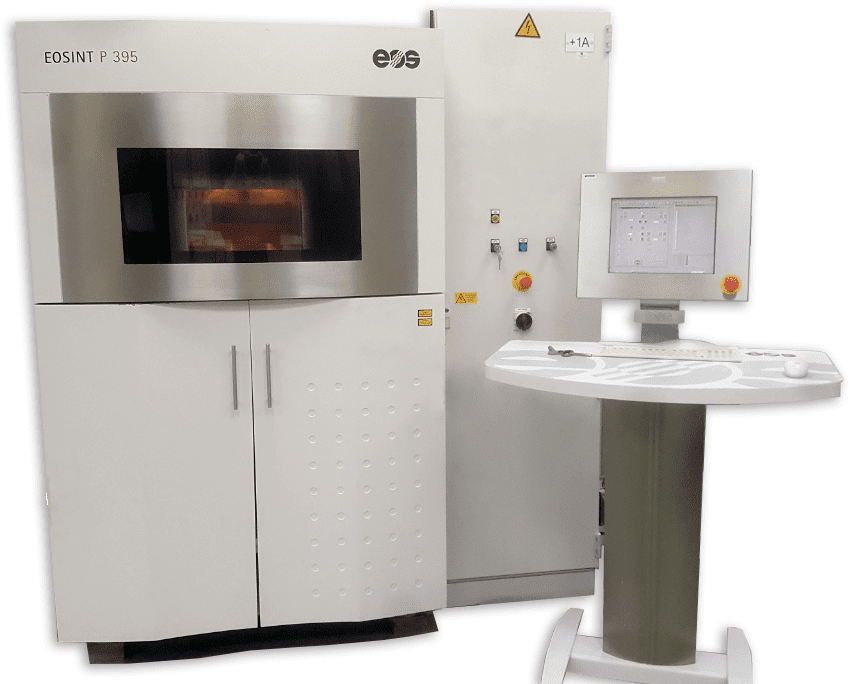
ATI uses a Selective Laser Sintering (SLS) printer which is an additive manufacturing procedure that uses a laser as the power source to sinter a specifically formulated powdered material. The SLS printer spreads a thin layer of the powdered material, typically nylon/polyamide, and uses a laser aiming at specific points in space defined by 3D CAD data binds the material together, creating a solid object. This machine not only produces quick turnaround prototype parts, tooling, and fixtures but is also a full production machine capable of running hundreds of pieces per batch. This extremely versatile piece of equipment gives ATI the ability to build custom, one of a kind parts in a very short timeframe.
Read more about how ATI's automotive manufacturing process increases flexible production here.
CNC Mill Machines
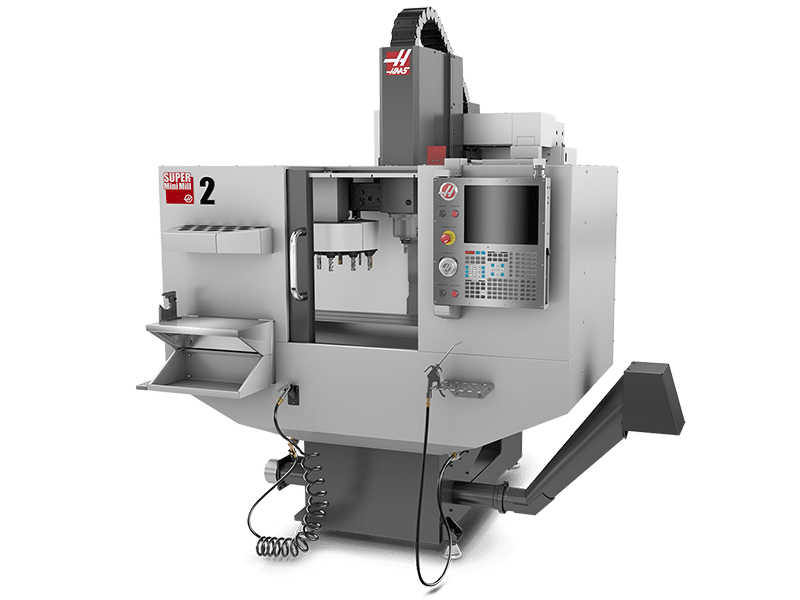
ATI specializes in low quantity, high performance production machining. ATI’s tight tolerance and attention to detail ensures the highest level of quality for all parts including out of the ordinary, hard to produce parts. ATI owns a wide range of mills and lathe equipment to manufacture anything from heat sinks to hardware product enclosures from material such as billet aluminum and sheet plastic. ATI manufactures parts for not only production, but prototypes, tooling, and fixtures for internal use.
PCB Technology
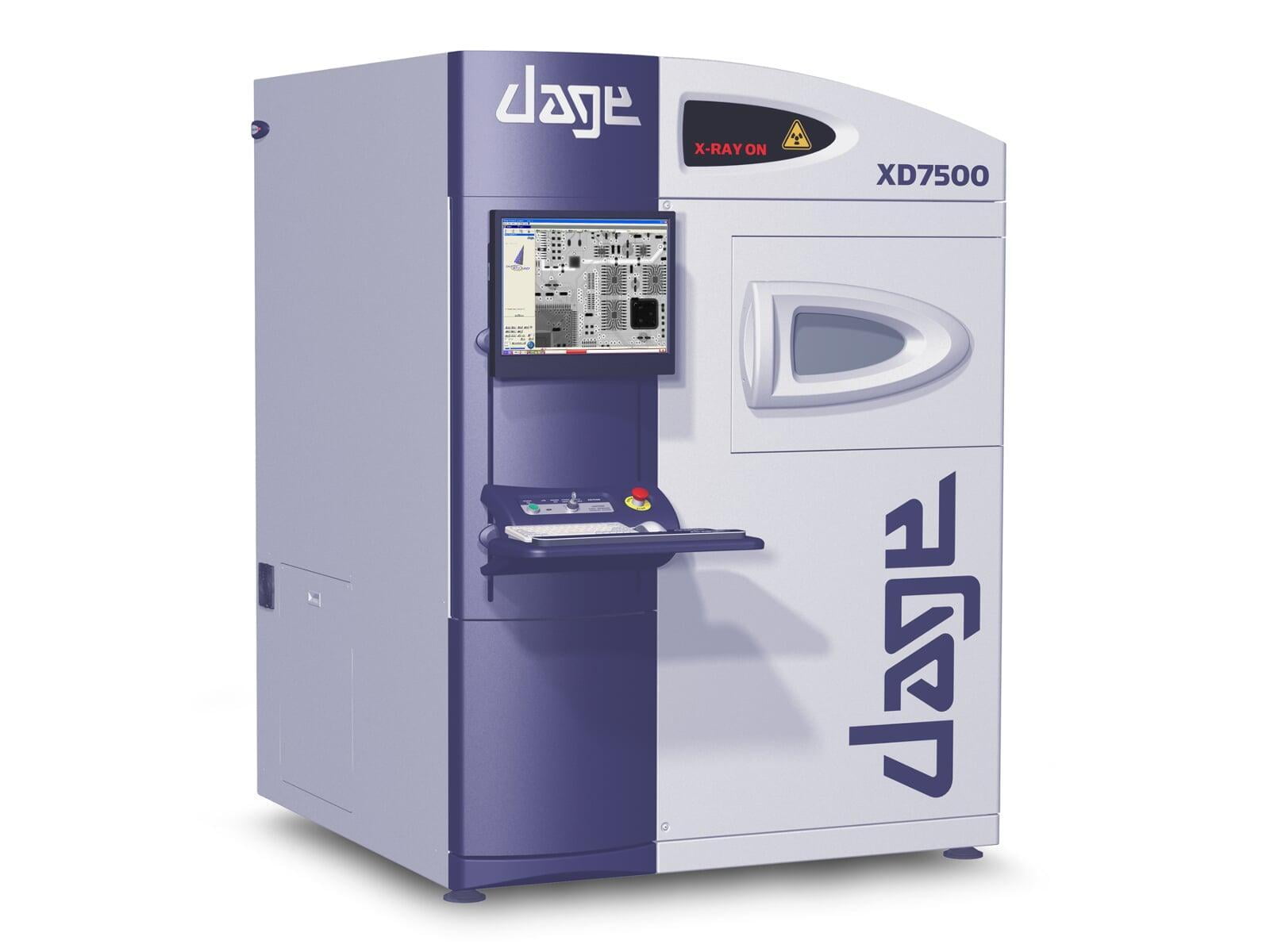
ATI’s circuit board designs are compact with high-density layouts which result in an end user product that can be placed in the smallest application areas, such as in-vehicle or test cells. The compact design and high durability are achieved using both multi layered and HDI sequential lamination processes. Ensuring our exceptional quality and high reliability from precision circuit boards is made possible with the use of X-ray technology. Our Dage X-ray machine provides Sub-Micron viewing capabilities allowing for the examination of solder joints and circuit board assembly quality not possible with typical inspection equipment.
Engineering Lab
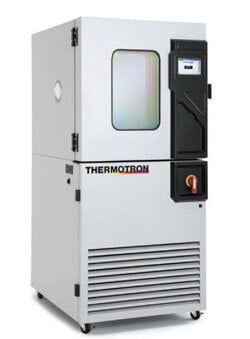